I should PM you more often when you're drunk at 1am.

Split moulds are my prefered method of casting for ease of manufature. Other companies - such as Forgeworld - use split mould for a great deal of their casting, for the reasons you state.
FW use split moulds for quite large model parts, including Reaver Titan legs!
Here is a pic of the backpacks from the FW ORK KOMMANDO CONVERSION SET. As you can see, they use the same process as above for *very* detailed items. The overall length of the casting is a bit under 120mm.
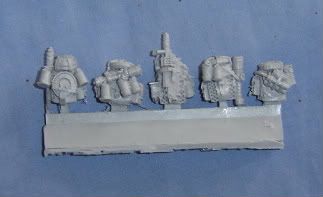
